Sustainable R&D
In 2021, EVRAZ R&D centres stepped up work to support the Group’s activities by utilising their global network of experts to create innovative steel products that better benefit customers.
Today, simply producing better products is not enough. To meet customer needs, the entire product life cycle needs to be taken into account. For example, using the electric arc furnace process with ferrous steel scrap as a raw material, EVRAZ produces rails with a substantially lower CO2 footprint compared with traditional steelmaking at integrated mills, as this requires less steel to extend product life under harsh conditions and enhance material performance.
Product development using virtual design has become increasingly important. Using data-driven AI models and digital twins, EVRAZ can improve production parameters more quickly, thereby accelerating product development.
Processes with a lower carbon footprint and accelerated deployment of product innovations contribute to greater sustainability.
Vanalytica© for accelerated product development
In the last 18 months, the EVRAZ VanadiumR&D group developed a software-driven consulting approach called Vanalytica© to support its customers and their needs. EVRAZ is partnering with a Cambridge-based start-up that is active in AI alongside a leading technology provider, which designs digital twins of existing production lines. State-of-the-art process models are being used to demonstrate the best ways to produce advanced steel grades that are cost effective and highly competitive. The team is focusing on accelerating product development through virtual process design, utilising the customer’s domain data in a secure and effective manner, while ensuring data privacy.
The digital twin approach creates an initial digital model of a mill. A huge library of empirical and proven metallurgical models is used to simulate the entire process of reheating, rolling and cooling and to predict material properties like grain size, strength and elongation.
AI offers a faster and more generic approach in this regard. This fast and disruptive method uses physical process data acquired in the rolling mill and properties from lab investigations. Combining AI with domain knowledge leads to surprisingly high R2 values that describe the confidence level of reality against the prediction of the model used.
EVRAZ North America
Heavy gauge line pipe: line pipe designs in North America aim to produce high-strength steel for large-diameter and thick-walled pipes due to their economic advantages. Safety and integrity are of utmost importance, particularly in cold operating environments, so toughness is also a critical property. With this in mind, previous investments in EVRAZ Regina’s steelmaking, rolling and pipe-making facilities offer a unique opportunity to be a market leader in these steel grades. To unlock this potential, the EVRAZ R&D team and Regina facility conducted a series of mill trials to develop an X80 product line with up to 0.75”wall thickness to enhance its toughness capabilities. Through data-driven decision-making, pilot-scale and mill trials, a combination of the alloy design and processing schedule provided both a high level of toughness and significant cost savings compared with initial estimates. This success led to EVRAZ securing an order from Coastal GasLink for 230,000 tonnes of this heavy gauge X80 product and over US$9 million in alloy cost savings, a landmark achievement for the heavy gauge programme and for EVRAZ.
The EVRAZ R&D team continues to diligently investigate new ways to improve the low temperature toughness of the heavy-gauge X70 and X80 grades. Modern data analytics, including the use of machine learning, is providing new insights into previous trials and production data.. Collaboration with leading academic partners, such as the University of British Columbia and McMaster University, has provided a greater understanding of these complex steel properties. Pilot-scale experiments through a partnership with CanmetMATERIALS, a Canadian government lab, offer a cost-effective method to study the alloys and process the possible changes. The combined efforts of all these research bodies and mill trials have boosted the resilience of EVRAZ high-strength and heavy gauge line pipes, ensuring that the Group is capable of meeting customers’ needs in the future.
As global efforts aim to achieve net zero emissions by 2050, the hydrogen- and other alternative energy-based economy is expected to grow rapidly. As one of the largest line pipe manufacturers in North America, EVRAZ NA is developing the expertise and products that will be needed in the near future, positioning itself as an industry leader.
EVRAZ NA is exploring new market opportunities, including hydrogen and CO2 pipelines as well as geothermal connections. The main objective is to develop technical capabilities to produce and qualify these products while also leading the industry through various collaborations and contributions to standards, codes and industry guidelines. As part of these efforts, R&D is working with industry partners, establishing collaboration local government research labs and academic research groups in both Canada and the US.
EVRAZ Vanadium R&D centre (East Metals AG, Zug)
The EVRAZ Vanadium R&D centre teamed up with EVRAZ Pueblo’s R&D team to develop a new high-strength wire steel grade. The driving force for developing the new wire is to produce new power transmission lines with longer spans between towers that ensure minimum sagging. The Vanalytica© approach was applied using AI. Within a short period, a new grade was developed based on several thousand data sets of pearlitic wire rod production. Research and qualification is ongoing and will support electric infrastructure investments by sustainably reducing the carbon footprint of the entire installation.
As part of long-term cooperation with the steel institute of RWTH Aachen University of Technology, EVRAZ is joining several publicly funded projects on infrastructural steel, heat treatment and the circular economy.
In addition, the EVRAZ Vanadium R&D centre has expanded its network through cooperation with the University of Perugia and the Italian Welding Institute. Leading Italian steel companies will support the project for further study.
EVRAZ ZSMK
EVRAZ has decided to establish a state-of-the-art R&D centre at EVRAZ ZSMK to research, improve and develop new rail products. The centre will be equipped with new testing facilities to conduct research using electron microscopy, dilatometry, tribometry, physical and mathematical modelling of rolling processes and rail heat treatment. EVRAZ seeks to achieve global leadership in the development of new rails and to expand its product range. In addition, EVRAZ ZSMK rails are produced through the electric arc furnace method using ferrous steel scrap as raw material, which results in the rails having a lower carbon footprint.
EVRAZ, together with Russian Railways, has completed operational testing of the new DT400IK rail. These rails which are made of hypereutectoid steel, have greater durability and are designed for operation on tracks with freight capacity per year of 80 mgt or more on sharp curves.
The tests were carried out on curves with a radius of 320 m or less and freight capacity per year of around 160 mgt. This combination represents some of the most severe operating conditions of Russian Railways, and the DT400IK rails showed a 15.8% reduction in wear compared with the basic DT350 rails. Although these results are not unexpected for rail wear,being confirmed by data from North American railways, EVRAZ will continue to develop new rails with improved wear resistance and a contact-fatigue life
EVRAZ fully threaded bar
In 2021, EVRAZ developed a new product: the fully threaded bar. Its main advantage is the ability to connect bars at any point, reducing connection time and providing benefits for the construction industry. During its development, the Group had to work under strict Russian code requirements concerning connections of fully threaded bars. EVRAZ worked with the R&D centre in North America to incorporate experiences from OCGT pipe connections and to transfer this behaviour to re-bars. Based on FEM modelling, thread parameters were modified to comply with Russian codes. The connection costs were also optimised. The R&D centre is continuously studying the behaviour of the re-bar connections through internal tests.
EVRAZ NTMK
A new R&D centre is being built at EVRAZ NTMK. The main goal is to support product-related research and new product development, since EVRAZ NTMK has the most broad product portfolio within the EVRAZ Group. High-quality beams, rails, wheels, grinding balls, merchant bars and other long products are being produced for the Russian market and export.
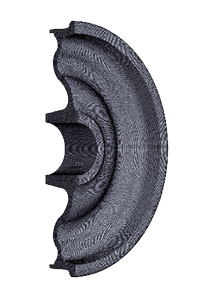
The new European wheel for ŠKODA passenger cars was developed to achieve a low stress level and increased strength. The EV006 wheel features increased operational reliability compared with the current Ba429 prototype. The disc’s special design ensures the wheel has greater wear resistance, which reduces customers’ operating costs and provides a positive contribution to sustainability.
Further R&D was carried out to modify the wheel material in combination with improved heat treatment modes for North American Class C+ freight cars. The increased wear resistance level improves the wheel life cycle due to hardness > 341HB, again in an effort to reduce customers’ operating costs.
Generating new ideas for the use of beams
One R&D project aims to study the composite behaviour of a precast concrete floor together with a hot rolled steel section structure under bending loads. The test results could help to create a composite structure of precast reinforced concrete slabs joined with hot-rolled steel profiles and be followed by the development of composite structure construction codes.
In 2021, the Group launched another R&D project with its partner Central Scientific Research Institute for Building Structures (CNIISK) to investigate how the initial residual stress distribution in EVRAZ hot-rolled beams affect the buckling reduction factor curve for elements subjected to compression. Residual stress in beams was also the subject of research conducted jointly with Austria’s Materials Center Leoben (MCL) in 2021. The simulation process and model will help the production line find a way to control stress distribution and tolerance following levelling process.
EVRAZ Tula
EVRAZ Vanady Tula’s R&D centre is primarily focused on decreasing vanadium losses in by-products. A brand new pilot plant has been built to support the transition from pure lab experiments to a full-scale production unit. The work performed in 2021 produced promising results. In 2022, the Group plans to finalise pilot plant tests and begin implementing the vanadium recycling facility project.
Another key goal is to support the VRB market with proper quality vanadium feed. In 2021, the Tula R&D centre completed work on high-purity oxide production technology. The centre proved that it is able to efficiently produce battery grade vanadium oxides. In 2022, the Tula R&D centre will focus on electrolyte production.